HiMB (Haesol Intelligent Monitoring Board)
HiMB collects data generated from various manufacturing-related systems, such as MES, WMS, HMI, QMS, SPC, and SCM, and builds an integrated DB suitable for businesses, using the latest tools through various devices (PC, mobile). It is an essential system for quick and accurate decision making that monitors the analysis and aggregated contents in real time for managers and engineers.
It is a powerful intelligent integrated analysis system that can be trusted by customers through better productivity and quality improvement by providing the key information required for smart factory operation in accordance with the factory reality clearly and quickly.
Configuration
Main Function : Interlocking with ERP, MES, WMS, HMI, QMS, SPC, SCM, real-time monitoring according to process status and inventory status, quality status, and production/shipment performance
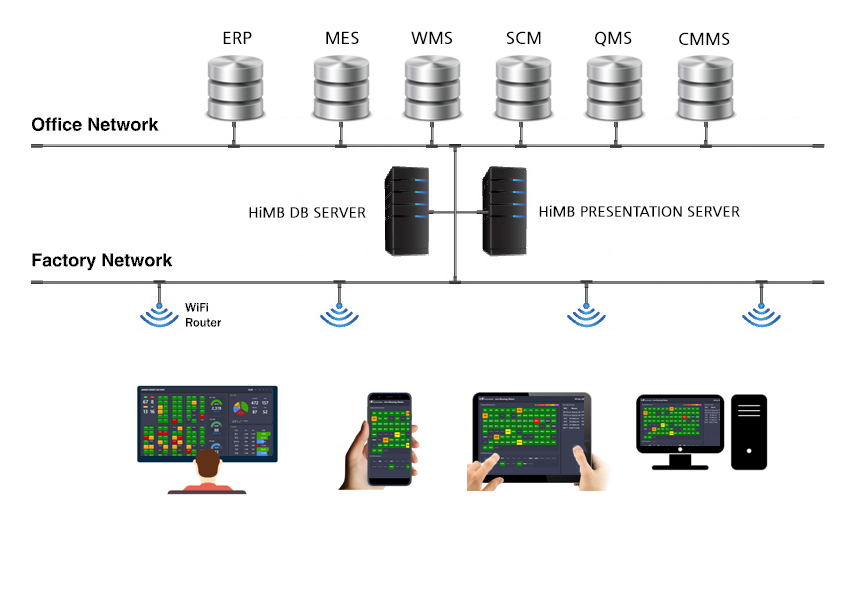
Samples
in Office
in Workcenter
in Control Room
on the Tablet
in Conference Room
in Workcenter
on the PC
on the Phone
Services
Many companies that have introduced IT systems such as ERP, MES, WMS, SPC, and QMS are getting a lot of help from their work, but they still do not get the necessary information and are still relying on manual aggregation or estimation. HiMB aggregates and implicitly displays the data needed for work in real time, helping you to easily make the necessary decisions right now.
HiMB is
maximizes the linkage and utility of various data owned by customers.
HiMB is
expressed in an intuitive configuration that is easy to understand and grasp at a glance.
HiMB is
a great help in decision-making because it can communicate key information clearly and quickly.
Production Line
It is possible to monitor the real-time production status of each workplace's performance against the target, and also to check whether there is operation/non-operation and the reason for non-operation in case of non-operation
In the event of a shortage of materials during production, the feeder can grasp key information such as missing materials and required amounts by workplace, stock amount by each storage location, and remaining order amount at a glance. It's possible.
In the trend, you can check the average of the previous year, this year, the previous month, the current month, and the performance trend compared to the one week plan. Also, the production status information for each product group is provided.
Quality Control
It provides key information such as how many items and quantities are pending in the quality inspection after production is complete, which items are the oldest, where is the production line, and what is the total pending amount.
In addition to the annual, monthly and daily trends, it is possible to immediately understand the current status of low-quality products and, in particular, which workplaces generate a lot of defects.
It is easy to know the share of each breakdown for what causes a lot of defects, and it is possible to monitor the delay history (delayed days) for countermeasures against defects and the person in charge.
Material Warehouse
The material receipt status is aggregated and expressed in real time. By separating general materials and special materials separately, you can check the average and daily trends of the previous year/this year/previous month/current month, and it is possible to understand at a glance what happens to suppliers with low stocking rates compared to orders.
It is possible to check in real time how the change in inventory amount and the trend of pending inventory are made by inventory storage location.
You can check the status of long-term inventory and information on how many months the inventory has elapsed at a glance, and it is possible to immediately check which inventory has been ordered even though there is long-term inventory.
Finished Goods Warehouse
You can check the shipment status of finished goods in real time. You can check the shipment trend of the previous year/this year/previous month/monthly average and weekly plan compared to the plan, and you can understand at a glance how the shipment rate performance by customer company is.
It is possible to monitor in real time whether there is stock in the warehouse compared to the same-day shipment plan and whether it is being inspected for shipment, waiting for inspection, or in production in case of shortage.
The long-term inventory status of the product warehouse is expressed by item, and you can check the shipment volume for the last 3, 6, and 9 months of the long-term inventory, so you can immediately check whether the item is being shipped continuously or is no longer shipped due to discontinuation.
소프트웨어 구성도
fastMES/POP은 안정적인 구조를 이루고 있으며 MES Core에 개별 서비스 모듈과 함께 기타 외부 모듈이 규격화 되어 결합됩니다. 생산환경이나 제조방식이 증설 및 변경이 되더라도 MES의 환경 설정 및 일부 수정을 통하여 신속한 대응이 가능 합니다.
기준정보 관리
- 공정코드 관리
- 자재/제품코드 관리
- 설비코드 관리
- 불량코드 관리
- BOM관리
- 파라미터/레서피 관리
- 스펙 관리
- 공급처/고객 관리
- 사용자/작업자 관리
- 시스템권한 관리
- 코드 마스터 관리
생산계획 관리
- 일일생산 계획
- LOT편성
- 라우트 조회
- 자재재고 현황
- 계획대비 실적
생산실적 관리
- 재공 현황
- 종합생산 현황
- 지시대비 투입/실적
- 생산 효율
- 생산 모니터링
- LOT추적
공정 관리
- 작업지시 조회
- 공정시작/완료
- 불량등록
- 공정변경
- 재공 조회
- LOT 추적
- LOT 분할/병합
- HOLD/HOLD해제
- 부적합보고/조회
- 설비 모니터링
설비 관리
- 예방 보전 관리
- 금형 및 치공구 관리
- 고장수리 관리
- 가동율 현황
- 비가동 현황
- 설비 효율
추적 관리
- LOT 추척 관리(정 전개)
- LOT 추적 관리(역 전개)
- 불량추적 관리
- 제조이력 추적 관리
출하 관리
- 제품 입고
- 출하 지시
- 출하 검사
- 포장
- 출하
- 반품
주요 화면
도입 효과
85%
리얼타임 처리기능
향상
74%
작업입력시간
단축
60%
PL법 대응능력
향상
56%
서류업무
감소
32%
리드타임
감소
25%
재고보유율
감소
운영적 효과
- 리드타임 단축
- 리얼타임 처리기능 향상
- 작업자 생산성 향상
- 생산 총 소요시간 단축
- 작업 입력시간 단축
- PL법 대응능력 향상
- 재공재고 감소
- 작업 표준화
- 제품 품질 향상
- 서류업무 감소
- 의사결정 지원
경영적 효과
- 제품 생산성 향상
- 제품 인도 신뢰성 향상
- 품질 향상
- 고객 서비스 향상
- IT 자동화에 따른 ROI 향상
- 자산 증가
- 의사결정 지원
- 재고부담 비용 감소
- 지시와 이행 일치
- 가동비 및 원가절감
- 재정적 지출 감소
- 가동비 및 원가절감