Schematic Diagram
MES serves as the information hub at the core of ERP (Enterprise Resource Planning), SCM (Supply Chain Management), and PDM (Product Data Management) systems.
It integrates production and delivery plans, as well as product and material information from ERP, SCM, and PDM, to manage overall production and manufacturing activities.
Additionally, MES controls DAS (Data Acquisition Systems) to facilitate production and equipment automation.
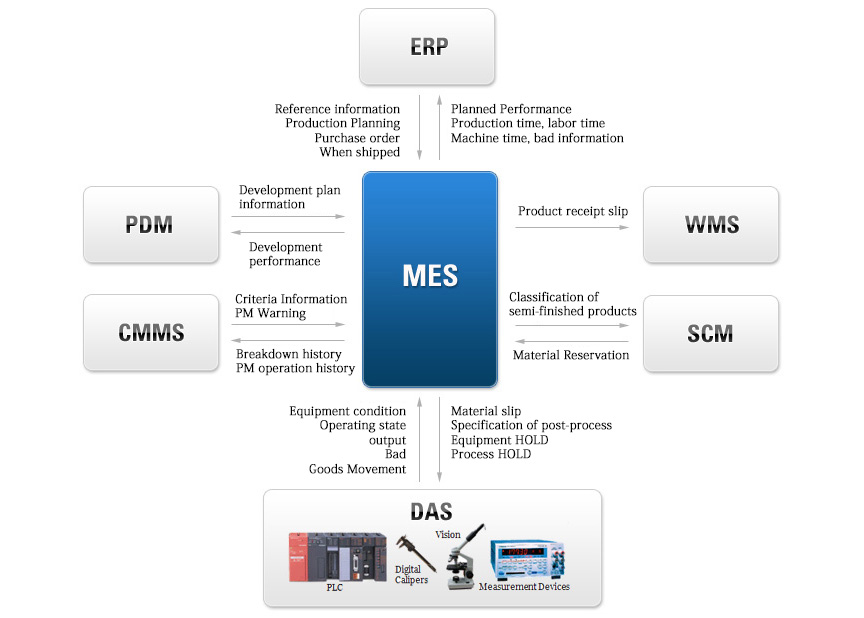
Hardware configuration diagram
Key features: Interworking with ERP such as SAP and Oracle, monitoring real-time process status, checking real-time trends of major process parameters through Industrial KIOSK, data interlocking using barcode and RF-ID, real-time tracking of LOT Traceability System , Production, shipment, etc.)
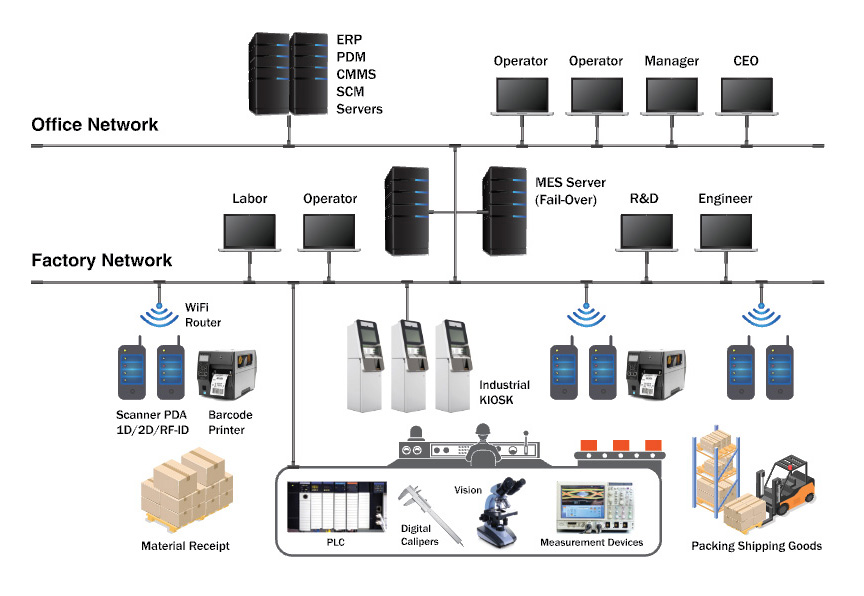
Process
Establish and distribute material supply and production plans according to sales plan and sales plan, and monitor movement of inter-process materials and work-in-progress. Real-time LOT tracking is also possible through defect management through quality control and overall flow control.
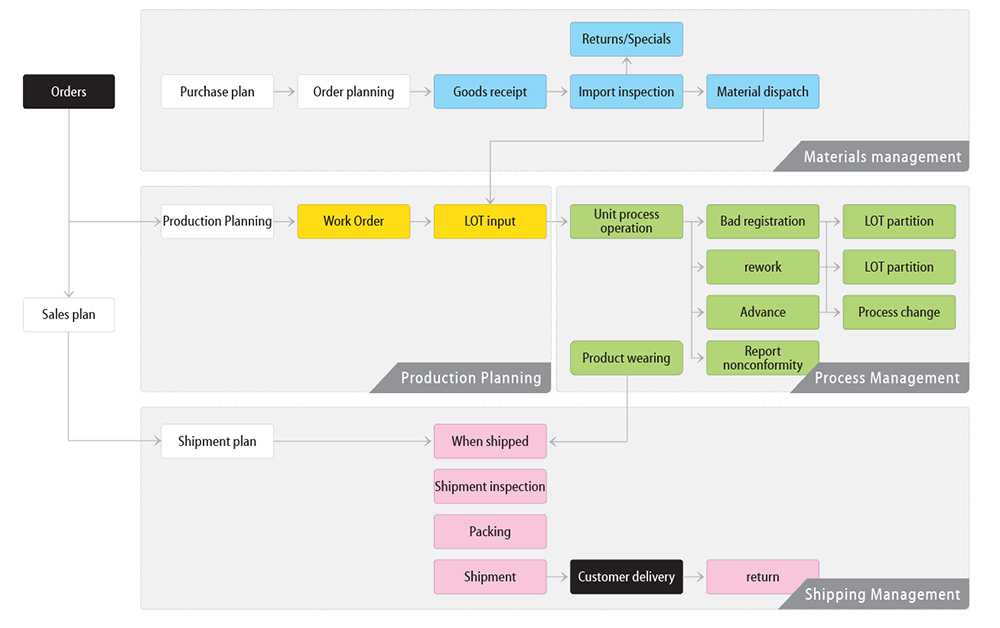
Software Configuration Diagram
FastMES has a stable structure, and other external modules are standardized together with individual service module in MES Core. Even if the production environment or manufacturing method is increased or changed, it is possible to respond quickly by setting environment and modifying MES
Base management
- Process code management
- Material / product code management
- Equipment Code Management
- Bad code management
- BOM management
- Parameter / Recipe Management
- Spec Management
- Source / Customer Management
- User / Operator Management
- System permissions management
- Code Master Management
Materials management
- Material receipt
- Import inspection
- Returns / Specials
- Material dispatch
Production Planning
- Daily Production Planning
- LOT knitting
- Route lookup
- Material Inventory Status
- Planned Performance
Production Performance
- Status of work
- Total Production Status
- Input versus instructions / performance
- Production efficiency
- Production monitoring
- LOT Tracking
Process management
- Displaying work order
- Process Start / Complete
- Bad registration
- Process change
- Re-worker check
- LOT Tracking
- LOT split / merge
- HOLD / HOLD Release
- Report inappropriate / Inquiries
- Facility monitoring
Facility management
- Preventive maintenance management
- Mold & tool management
- Troubleshooting
- Availability Rate
- Non-moving status
- Facility efficiency
Quality Management
- Defect status
- Parameter analysis
- Yield status
Tracking management
- LOT tracking management (static deployment)
- LOT tracking management (reverse deployment)
- Bad Tracking Management
- Manufacturing history tracking management
Shipping Management
- Goods Receipt
- Shipment instruction
- Shipment inspection
- Packing
- Shipment
- return
Main Screen
Effect of introduction
85%
Improved real-time processing
74%
Shorten work input time
60%
Improved ability to respond to PL law
56%
Decrease in paperwork
32%
Lead time reduction
25%
Decrease inventory hold
Operational effects
- Reduce lead time
- Improved real-time processing
- Increase worker productivity
- Reduced total production time
- Shorten work input time
- Improved ability to respond to PL law
- Reduced inventory
- Standardize work
- Product quality improvement
- Decrease in paperwork
- Decision Support
Business Effect
- Product Productivity Improvement
- Improving product reliability
- Quality improvement
- Improve customer service
- Improving ROI through IT Automation
- Asset growth
- Decision Support
- Reduced inventory cost
- Directive and transition agreement
- Operation cost and cost reduction
- Decrease financial expenditure
- Operation cost and cost reduction